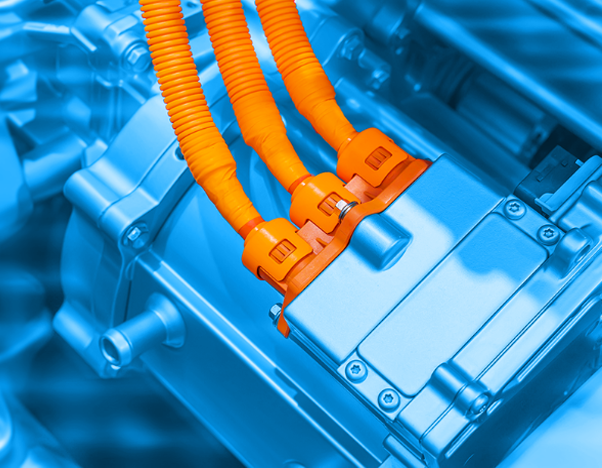
The customer
Registered office: Koenigsberg, Germany
Employees: up to 5,000
Sector: Development and manufacture of system components made of plastic and metal
Whether manufacturer or supplier - more and more companies from the automotive sector and manufacturing industry are demanding direct access to telemetry data from the machines involved in production. Even individual processes should be able to be analyzed with their own tools. The demands on the digital skills of business partners are correspondingly high. An experience that FRÄNKISCHE also had to make.
Customer
FRÄNKISCHE Rohrwerke Gebr.
Kirchner GmbH & Co. KG
Industry
Development and manufacture of system components made of plastic and metal
Seat
Koenigsberg, Germany
Partner
Microsoft Germany GmbH
Company size
up to 5,000 employees
Products and Services
Microsoft Azure Services
& Azure Industrial IoT

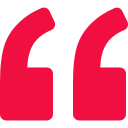
„We now have detailed insights into the states and processes of the individual machines. Just collecting the data and analyzing it is enormously valuable for each of our departments – for example in quality assurance.“
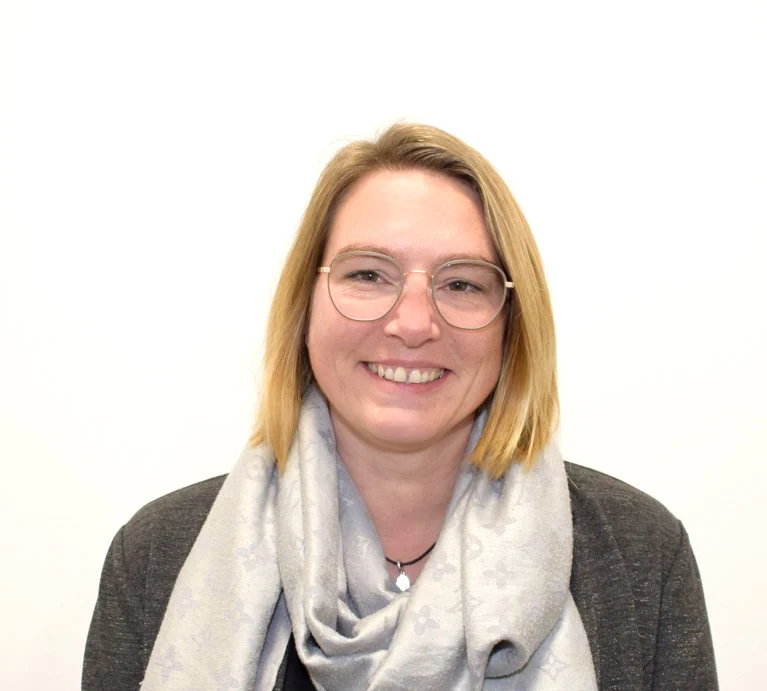
Digital Transformation Office / FRÄNKISCHE
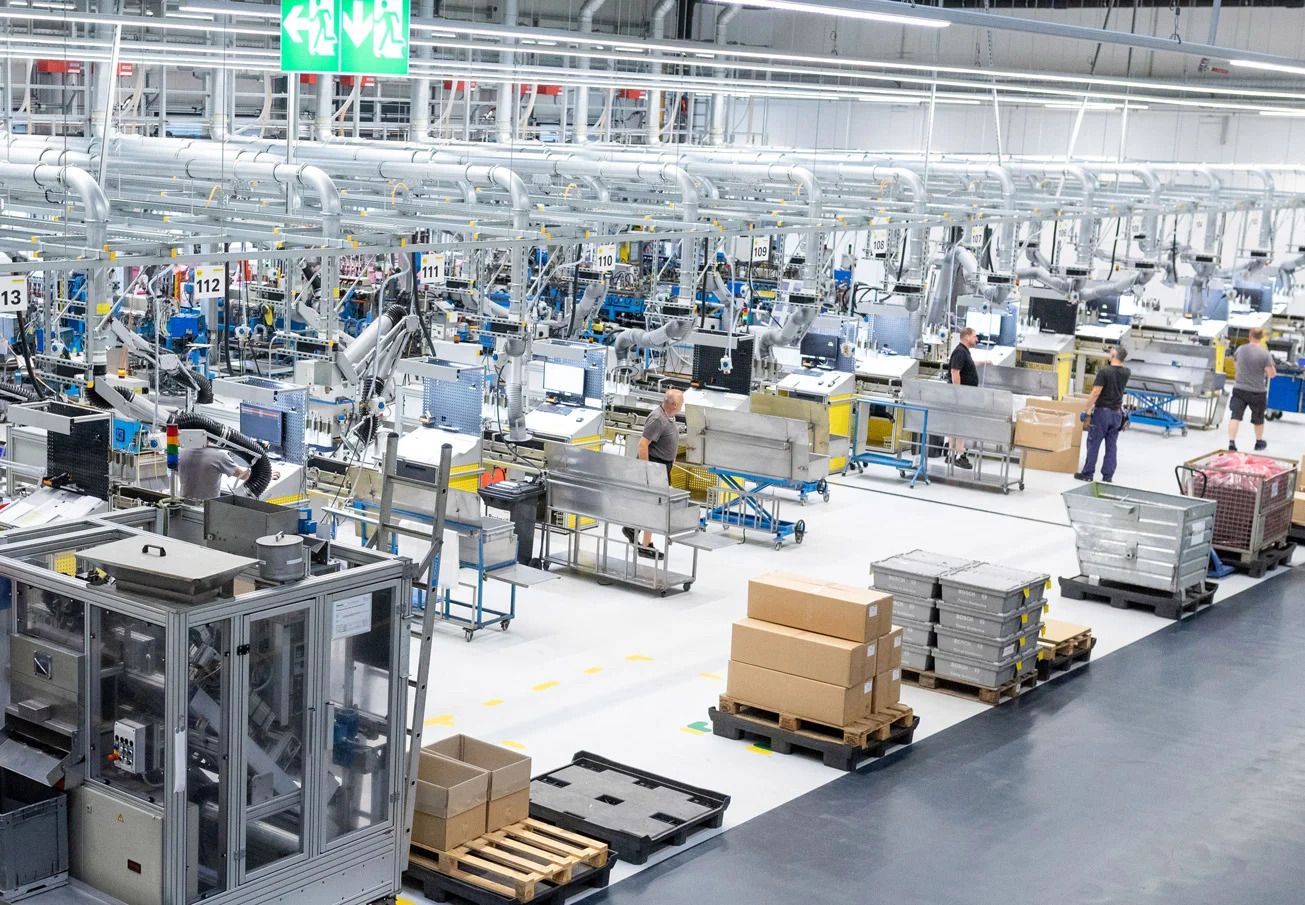
The challenge
The company had previously invested little in digital technologies. IoT concepts were just as non-existent as cloud solutions. “All of this was really new territory for us,” explains Stefan Endorff, Team Leader Digital Transformation Office. “However, our customers require precise tracking of each individual component produced. And the best way to do that is with modern IoT monitoring.” The company was therefore looking for a partner who could drive forward the digitization of the industrial company. It quickly became clear: daenet is this partner.
The solution
Together with daenet, FRÄNKISCHE has broken new digital ground and set up a modern IoT platform for planning, monitoring and recording production processes via Microsoft Azure. This enables cross-site system control. Thanks to the intelligently networked machines and systems, the tracking of the telemetry data takes place efficiently and fully automatically - throughout the entire production process - from the selection of materials to the thermal oven to the assembly and delivery of the pipes.
The solution contains a complex user guide through various processes for material recording - for example with the help of barcode scanners or the web app user interface. Among other things, this facilitates:
-
the raw material management and the distribution of the parking spaces of a factory
-
the configuration of the raw material flow via the pipe connections from the storage locations to the machines.
-
the validation and tracing of the current connections at the start of a production order as well as the raw material at the beginning of a production order and at its end.
The result: The process contained in the production order (n machines, n stations, n locations) can be optimally configured and the corresponding machines optimally controlled. This includes the connection of various production machines with the help of Azure IoT Edge Module (primarily using the OPC UA protocol), the implementation of a user interface for the management of the raw material flow and a production feedback user interface as well as the connection of industrial scanners to the platform using Azure Internet of Things
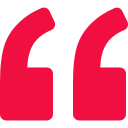
„Customers value our high-quality products. In the innovative automotive industry in particular, however, this is not enough to remain competitive. Intelligently networked systems that enable integrated work across the entire supply chain are almost even more important. SmartFactory makes the crucial difference here.“
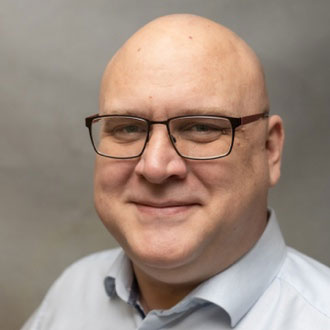
Team Leader Digital Transformation Office / FRÄNKISCHE
The use
Smart factory solutions such as data tracking ensure more transparency and efficiency in the production process and thus in the entire business process. Because customers can call up the analyzes over many years, interpret them and use them as an important indicator for production control. All relevant key figures are available on the UI interface and can be used to optimize the production processes. The risk of production errors is also minimized. This conserves resources, saves costs and is an important component of quality management. The real benefit, however, lies in how customers perceive it. Because they appreciate the new digital innovative strength of the company and regard FRÄNKISCHE as a strong partner of the automotive and manufacturing industries - today and in the future.
Die Lösungsdiagramme
(zum Vergrößern klicken)
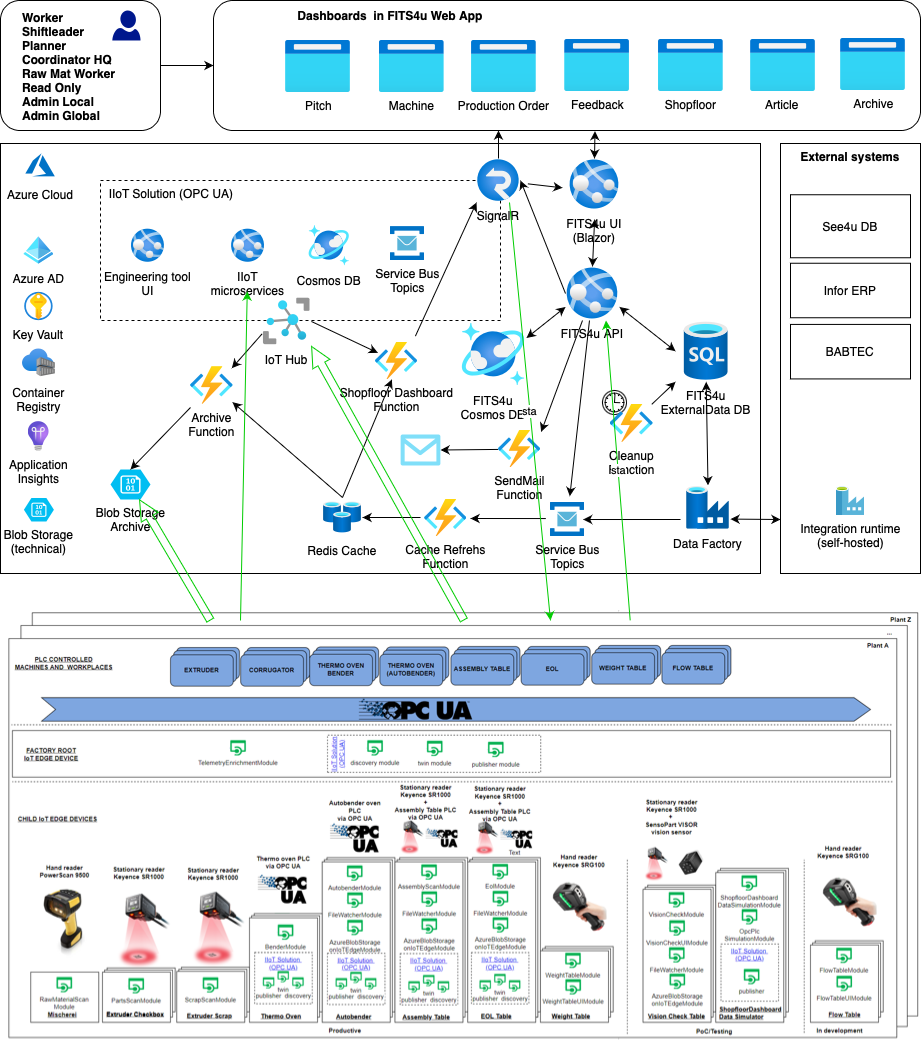
Direct line to our experts
Any questions? - We are here for you!
Get in direct contact with our digital solutions specialists.
In co-operation with:
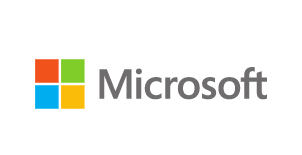
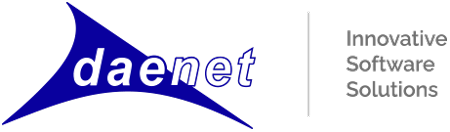